SIGNUM Computer GmbH
Lena-Christ-Str. 50
D-82152 Planegg-Martinsried
D-82152 Planegg-Martinsried
Rechtsform: | GmbH |
Handelsregister: | HRB 69901 |
Registergericht: | Amtsgericht München |
Geschäftsführung: | Dr.-Ing. Alfred Vogel |
Ust.-ID: | DE129460180 |
Gesellschafter/-in: | Dr.-Ing. Alfred Vogel |
Die Angaben im Impressum unterliegen dem Verantwortungsbereich des jeweiligen Unternehmens. |
- Impressum
Einfache Konturprüfung / Inspektion auch dicker Bleche
26.06.2017
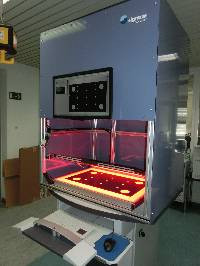
Die größten zu prüfenden Bauteile können 675 x 450 mm² groß sein. Bei Blechen mit einer Dicke von 2mm sind kleine Bohrungen unterhalb eines Durchmessers von 1mm auch bis zum Bauteilerand prüfbar.
Stanzteile können häufig viele Bohrungen und Konturvariationen aufweisen. Das Fehlen einer kleinen Bohrung oder auch eine unvollständige Stanzung kann leicht übersehen werden und zu Produktionsausfällen oder Schlimmerem führen. Problematisch sind dicke Dichtungen, die kleine Bohrungen aufweisen, deren Durchmesser kleiner sind als die Materialstärke. Für solche produktionstypische Anforderungen hat Signum aus München einen halbautomatischen Prüfplatz entwickelt.
Stanzwerkzeuge arbeiten im Sekundentakt. Kommt es zu einem Bruch dieses Werkzeugs verändert sich im Allgemeinen die Sollkontur und im Sekundentakt wird Schrott produziert.
Um dem Maschinenbediener ein einfach zu bedienendes und schnelles Prüfwerkzeug zur Hand zu geben hat Signum einen optischen Stehprüfstand für die raue Produktionsumgebung entwickelt. Der Bediener braucht lediglich den Bauteiltyp auswählen, das Bauteil annähernd mittig auf die Leuchtplatte legen und die Prüfung starten.
Noch einfacher ist es, wenn zu dem Bauteil ein Datenblatt oder ähnliches existiert, auf dem ein Strich- oder 2D-Code das Bauteil definiert. Durch ein erstes Lesen des Codes wird der Datensatz bzw. das Prüffile des Bauteils geladen. Ein Bild des Bauteils zeigt an, wie es aufgelegt werden soll, was in einem Livebild überprüft werden kann. Durch eine zweite Codelesung (oder manuell) wird die Prüfung ausgelöst. Im niO-Fall werden die Fehler grafisch verdeutlicht und die prozentualen Abweichungen jeder Bohrung angegeben.
Auch das Einlernen eines neuen Bauteils wurde auf das Nötigste reduziert. Es müssen lediglich die etwaigen Außenmaße des Bauteils eingegeben werden. Der Name des Prüffiles kann über einen Code aber auch händisch eingegeben werden. Die Software ermittelt dann automatisch alle Konturen eines Master-Bauteils sowie die Flächen und Positionen aller innen liegenden Stanzungen. Die Schwellwerte zum Fehlerfall werden defaultmäßig gesetzt, können aber auch nachträglich für jede einzelne Bohrung geändert werden. Kleine Bohrungen werden höherschwellig parametriert. Das Erstellen oder Ändern eines Prüffiles ist durch ein Passwort schützbar. Zwecks Nachverfolgbarkeit werden alle Prüfbilder dokumentiert.
Dünne Bleche, die sich aufwölben können, werden unter eine Glasplatte gelegt, die sie niederhält. Das händische Anheben der Glasplatte wird durch Gasdruckfederelemente vereinfacht. Dicke Bauteile, z. B. Getriebedichtplatten, die sich nicht aufwölben, werden einfach auf die Glasplatte gelegt.
Die Bauteile müssen so geprüft werden, wie sie auch eingelernt wurden, das heißt entweder unter der Niederhalterglasplatte oder darauf. Um eine Fehlbedienung auszuschließen, wird dies mit einem Sensor überprüft.
Die Leuchtplattengröße beträgt 725 x 500 mm², sodass Objekt bis zu einer maximalen Größe von 675 x 450 mm² geprüft werden können. Die Positionstoleranz insbesondere kleinerer Prüfobjekte beträgt ± 50 mm bei einem Verdrehwinkel von 360°.
Das Objektfeld wird von zwei hochauflösenden Kameras mit je 3840 x 2748 Pixel aufgenommen und zu einem Bild zusammengefügt wird. Damit beträgt die Auflösung des resultierenden Bildes 0,13 mm pro Pixel.
Es werden zwei Kameras (statt einer noch höher auflösenderen) eingesetzt, um möglichst gerade durch dicke Prüfobjekte hindurch schauen zu können, bzw. den Öffnungswinkel der Optik klein zu halten.
Um den Öffnungswinkel noch weiter zu reduzieren, wurde der Arbeitsabstand zu den Kameras mit 2,6 m möglichst groß gewählt. Damit der komplette Prüfstand auch in Räumen mit „normaler“ Höhe bis 2,4 m aufgestellt werden kann, schauen die Kameras über einen Spiegel auf die Leuchtplatte. Damit befinden sie die Kameras hinter und unter der Leuchtplatte im Schaltschrank, wo sich auch die komplette Elektronik befindet.
Auf diese Weise beträgt der maximale Winkel, mit dem am Rand des Bildfeldes durch ein Prüfobjekt geschaut wird, 3,7°. Bohrungen mit einem Durchmesser von etwa einem Drittel der Prüfobjektdicke können so überprüft werden. Durch die hohe Pixelauflösung werden Fehler ab einer Fläche von ca. 0,15 mm² und Konturabweichungen ab ca. 0,4 mm erkannt.
Das komplette System wird schlüsselfertig inklusive Einweisung ausgeliefert und installiert.
Stanzwerkzeuge arbeiten im Sekundentakt. Kommt es zu einem Bruch dieses Werkzeugs verändert sich im Allgemeinen die Sollkontur und im Sekundentakt wird Schrott produziert.
Um dem Maschinenbediener ein einfach zu bedienendes und schnelles Prüfwerkzeug zur Hand zu geben hat Signum einen optischen Stehprüfstand für die raue Produktionsumgebung entwickelt. Der Bediener braucht lediglich den Bauteiltyp auswählen, das Bauteil annähernd mittig auf die Leuchtplatte legen und die Prüfung starten.
Noch einfacher ist es, wenn zu dem Bauteil ein Datenblatt oder ähnliches existiert, auf dem ein Strich- oder 2D-Code das Bauteil definiert. Durch ein erstes Lesen des Codes wird der Datensatz bzw. das Prüffile des Bauteils geladen. Ein Bild des Bauteils zeigt an, wie es aufgelegt werden soll, was in einem Livebild überprüft werden kann. Durch eine zweite Codelesung (oder manuell) wird die Prüfung ausgelöst. Im niO-Fall werden die Fehler grafisch verdeutlicht und die prozentualen Abweichungen jeder Bohrung angegeben.
Auch das Einlernen eines neuen Bauteils wurde auf das Nötigste reduziert. Es müssen lediglich die etwaigen Außenmaße des Bauteils eingegeben werden. Der Name des Prüffiles kann über einen Code aber auch händisch eingegeben werden. Die Software ermittelt dann automatisch alle Konturen eines Master-Bauteils sowie die Flächen und Positionen aller innen liegenden Stanzungen. Die Schwellwerte zum Fehlerfall werden defaultmäßig gesetzt, können aber auch nachträglich für jede einzelne Bohrung geändert werden. Kleine Bohrungen werden höherschwellig parametriert. Das Erstellen oder Ändern eines Prüffiles ist durch ein Passwort schützbar. Zwecks Nachverfolgbarkeit werden alle Prüfbilder dokumentiert.
Dünne Bleche, die sich aufwölben können, werden unter eine Glasplatte gelegt, die sie niederhält. Das händische Anheben der Glasplatte wird durch Gasdruckfederelemente vereinfacht. Dicke Bauteile, z. B. Getriebedichtplatten, die sich nicht aufwölben, werden einfach auf die Glasplatte gelegt.
Die Bauteile müssen so geprüft werden, wie sie auch eingelernt wurden, das heißt entweder unter der Niederhalterglasplatte oder darauf. Um eine Fehlbedienung auszuschließen, wird dies mit einem Sensor überprüft.
Die Leuchtplattengröße beträgt 725 x 500 mm², sodass Objekt bis zu einer maximalen Größe von 675 x 450 mm² geprüft werden können. Die Positionstoleranz insbesondere kleinerer Prüfobjekte beträgt ± 50 mm bei einem Verdrehwinkel von 360°.
Das Objektfeld wird von zwei hochauflösenden Kameras mit je 3840 x 2748 Pixel aufgenommen und zu einem Bild zusammengefügt wird. Damit beträgt die Auflösung des resultierenden Bildes 0,13 mm pro Pixel.
Es werden zwei Kameras (statt einer noch höher auflösenderen) eingesetzt, um möglichst gerade durch dicke Prüfobjekte hindurch schauen zu können, bzw. den Öffnungswinkel der Optik klein zu halten.
Um den Öffnungswinkel noch weiter zu reduzieren, wurde der Arbeitsabstand zu den Kameras mit 2,6 m möglichst groß gewählt. Damit der komplette Prüfstand auch in Räumen mit „normaler“ Höhe bis 2,4 m aufgestellt werden kann, schauen die Kameras über einen Spiegel auf die Leuchtplatte. Damit befinden sie die Kameras hinter und unter der Leuchtplatte im Schaltschrank, wo sich auch die komplette Elektronik befindet.
Auf diese Weise beträgt der maximale Winkel, mit dem am Rand des Bildfeldes durch ein Prüfobjekt geschaut wird, 3,7°. Bohrungen mit einem Durchmesser von etwa einem Drittel der Prüfobjektdicke können so überprüft werden. Durch die hohe Pixelauflösung werden Fehler ab einer Fläche von ca. 0,15 mm² und Konturabweichungen ab ca. 0,4 mm erkannt.
Das komplette System wird schlüsselfertig inklusive Einweisung ausgeliefert und installiert.